Plastic extrusion for complex profiles and custom designs
Plastic extrusion for complex profiles and custom designs
Blog Article
Recognizing the Essentials and Applications of Plastic Extrusion in Modern Production
In the world of modern manufacturing, the technique of plastic extrusion plays an important function. Unraveling the principles of this procedure exposes the real convenience and potential of plastic extrusion.
The Fundamentals of Plastic Extrusion Process
While it might appear complex, the fundamentals of the plastic extrusion procedure are based on fairly straightforward principles. It is a production process wherein plastic is thawed and after that shaped right into a continual account through a die. The plastic extrusion procedure is thoroughly used in different industries due to its efficiency, versatility, and cost-effectiveness.
Various Sorts Of Plastic Extrusion Techniques
Building upon the fundamental understanding of the plastic extrusion procedure, it is essential to explore the various strategies associated with this production method. The 2 primary techniques are profile extrusion and sheet extrusion. In account extrusion, plastic is thawed and created into a continual account, typically made use of to develop pipes, poles, rails, and home window frames. In comparison, sheet extrusion creates big, flat sheets of plastic, which are generally additional refined right into products such as food packaging, shower curtains, and automobile components. Each method calls for specialized equipment and specific control over temperature level and stress to make certain the plastic maintains its shape during cooling. Comprehending these methods is crucial to making use of plastic extrusion efficiently in contemporary manufacturing.

The Role of Plastic Extrusion in the Automotive Sector
A frustrating majority of components in modern automobiles are items of the plastic extrusion process. This process has actually transformed the vehicle industry, changing it into a much more reliable, economical, and flexible manufacturing market. Plastic extrusion is mostly used in the manufacturing of different automobile elements such as bumpers, grills, door panels, and dashboard trim. The procedure provides an uniform, regular result, making it possible for manufacturers to produce high-volume get rid of excellent precision and marginal waste. The agility of the extruded plastic components adds to the general decrease in vehicle weight, enhancing fuel effectiveness. The longevity and resistance of these parts to warmth, cold, and impact boost the longevity of vehicles. Therefore, plastic extrusion plays a critical function in automobile manufacturing.

Applications of Plastic Extrusion in Durable Goods Manufacturing
Beyond its significant impact on the auto industry, plastic extrusion shows equally reliable in the world of customer items making. This process is important in creating a wide selection of items, from food anchor packaging to home appliances, playthings, and also medical devices. The versatility of plastic extrusion enables producers to design and generate intricate forms and sizes with high accuracy and performance. Furthermore, due to the recyclability of several plastics, squeezed out elements can be reprocessed, lowering waste and expense. The flexibility, adaptability, and cost-effectiveness of plastic extrusion make it a recommended selection for numerous durable resource goods suppliers, contributing significantly to the sector's growth and innovation. Nevertheless, the environmental effects of this extensive usage require mindful consideration, a subject to be talked about further in the succeeding section.
Ecological Influence and Sustainability in Plastic Extrusion
The prevalent use plastic extrusion in manufacturing invites analysis of its ecological implications. As a process that regularly uses non-biodegradable materials, the environmental influence can be substantial. Power intake, waste production, and carbon discharges are all problems. Market developments are enhancing sustainability. Reliable machinery reduces power usage, while waste monitoring systems reuse scrap plastic, lowering basic material needs. In addition, the development of eco-friendly plastics provides a much more environmentally friendly choice. Regardless of these improvements, even more advancement is needed to minimize the ecological impact of plastic extrusion. As society leans in the direction of sustainability, makers need to adapt to remain practical, highlighting the significance of continuous research and development in this area. check that
Verdict
In verdict, plastic extrusion plays a vital duty in contemporary production, specifically in the auto and customer products fields. Recognizing the basics of this process is crucial to maximizing its benefits and applications.
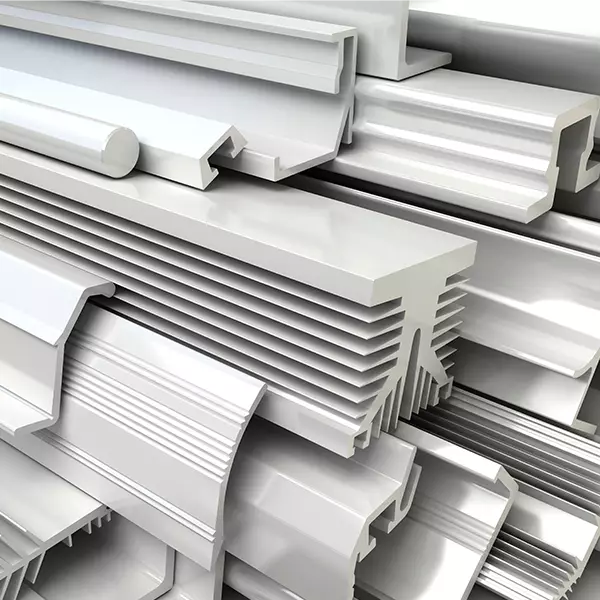
The plastic extrusion process is thoroughly used in different industries due to its cost-effectiveness, versatility, and effectiveness.
Building upon the standard understanding of the plastic extrusion procedure, it is required to explore the different methods involved in this manufacturing technique. plastic extrusion. In contrast, sheet extrusion produces large, level sheets of plastic, which are commonly additional refined into items such as food packaging, shower curtains, and automobile components.An overwhelming bulk of components in modern automobiles are items of the plastic extrusion process
Report this page